Cessna Citation 501 Flight Manual

The highly popular Cessna 500 Citation and 500 Citation I pioneered the entry level light business jet market, and their success formed the basis for the world's largest family of corporate jets. Cessna became the first of the big three American manufacturers (Piper, Beech and Cessna) to develop a jet powered transport. In October 1968 Cessna announced its plans to build a new eight place jet powered business aircraft that would be capable of operating into airfields already served by light and medium twins. Dubbed the Fanjet 500, the prototype flew for the first time on September 15 1969. Soon after the new little jet was named the Citation. A relatively long development program followed, during which time a number of key changes were made to the design including a longer forward fuselage, repositioned engine nacelles, greater tail area and added dihedral to the horizontal tail. In this definitive form the Citation was granted FAA certification on September 9 1971.
Improvements including higher gross weights and thrust reversers were added to the line in early 1976, followed shortly after by the introduction of the enhanced Citation I later that same year. Features of the Citation I were higher weights, JT15D-1A engines and an increased span wing. A further model to appear was the 501 Citation I/SP, which is certificated for single pilot operation.
The I/SP was delivered in early 1977. Production of the Citation I ceased in 1985, its place in the Citation line left vacant until the arrival of the CitationJet (described separately) some years later. Direct developments of the Citation were the Citation II (now Citation Bravo) and Citation V (now Citation Ultra Encore).
Products, Inc Maintenance Manual 21-50-00 May 15/95 Page 2 Two evaporator/blower units are located in the aft cabin at the spar (at floor level) within the aircraft interior. They provide cooling airflow for the cabin and cockpit areas of the interior. The left evaporator is ducted to provide cooling airflow to the flight crew through a floor mounted air outlet or through dedicated ducting at the pilots and co- pilots control stick. The right evaporator is ducted to provide cooling airflow to the aft cabin through a floor mounted air outlet. Both evaporators are of a design wherein the cabin air is drawn into the evaporator coil and the fan then delivers the conditioned air to the cabin.
This recirculating system continues to dry and cool the air each time it passes through the evaporator. Moisture removed from the air by the cold coil (condensate) is collected within the evaporator housing and is forced overboard. Each evaporator is equipped with a thermal expansion valve which regulates the amount of refrigerant entering the coil to provide optimum cooling effect. The evaporator blowers can be operated in the FAN position to recirculate cabin air without cooling.
Each blower is operated from an independent fan speed control. The plumbing which connects the compressor, condenser and the evaporators, consists of rubber based hoses with a nylon barrier. The fittings are permanently swaged onto the hoses. All fittings are o-ring type connections with sealant on the fitting mating surfaces to prevent refrigerant leaks. Two R134a service valves are located near the compressor/condenser pallet assembly.
They are sized differently to avoid incorrect cross-connecting when gaining access to the plumbing for system recharging. On the ground, the electrical system allows operation of the air conditioning system from either aircraft generator or from an active GPU prior to engine start. System safety features include electrical interlocking and load shedding. In flight, the air conditioning system can be operated from the aircraft electrical system only with both generators on line. Loss of either generator will automatically shed the air conditioning system electrical loads except for the minimal loads of the evaporator fans. The entire air conditioning refrigerant loop is protected against over pressure conditions by two separate safety devices. The first device is a binary high/low pressure switch that activates in the event of an overpressure and is on the compressor discharge port.
This switch will open at approximately 350 PSIG and will interrupt power to the compressor control circuit. This in turn will de-energize the compressor motor relay and remove power to the compressor motor. The refrigerant system pressures will then drop. The switch will also interrupt power to the compressor control circuit under low pressure conditions. The second overpressure safety device is a fuse plug which will vent the system refrigerant safely overboard in the event of a system pressure in excess of 425 PSIG. It is located on the receiver/drier.
Products, Inc Maintenance Manual 21-50-01 May 15-95 Page 1 ELECTRICAL DESCRIPTION AND OPERATION 1. GENERAL The air conditioning system consists of one high energy compressor/condenser drive motor and two centrifugal evaporator blowers. The system is controlled by a mode switch with Air Conditioning Off and Fan Only position. Each evaporator has a high and low position switch. A blue indicator light will illuminate whenever the compressor/condenser is selected. The system incorporates a binary pressure switch to sense an over pressure or under pressure condition in the system.
The air conditioning system in controlled by a Logic Card which monitors generator, GPU and battery inputs to ensure operation or shedding of the system if a fault exists. The system is protected by a 15 amp control and blower breaker and a 100 amp breaker for the compressor/condenser drive motor. This section of the maintenance manual describes the electrical system and presents electrical troubleshooting procedures.
An Illustrated Parts List is included in Figure 1. LOAD/SHED DESCRIPTION The system incorporates a logic control PC card that enables the system to operate or be shed under various conditions. The table below shows operation under various conditions. CONDITIONS EVAP FANS COMP/COND Gnd Power Cart/On On On Gnd Power Cart Connected/Off On Off Battery Only On Off One Generator on Ground On On Both Generators on ground On On Refrigerant Over/Under Pressure On Off One Generator in Flight On Off Both Generators in Flight On On. Products, Inc Maintenance Manual 21-50-01 May 15/95 Page 101 TROUBLESHOOTING 1. GENERAL The following procedures are used for troubleshooting the electrical system and the electrical interfaces with the other assemblies of the air conditioning system. TOOLS AND EQUIPMENT Designation Ref.
Qty Remarks Service Pressure Gauge Comm. 1 None Multi-meter Comm. 1 None 28vdc Source A/R None 3.
ELECTRICAL TROUBLESHOOTING PROCEDURES (REF. 1) NOTE: Always attach a service gauge set to system prior to beginning trouble shooting to insure proper refrigerant charge is present.
Air Condition Selected, Compressor/Condenser Motor Does Not Turn. Connect service pressure gauge to service ports located near compressor/condenser pallet.
Connect ground power to aircraft. Select air conditioning system to ON. Check that load shed start conditions in the Description and Operation paragraph are met.
Check for power at comp/cond relay located on the pallet assembly, if not present check 100A circuit breaker (3) Replace if necessary. Check continuity of pressure switch (Ref.
21-50-02 IPL Fig. If no continuity and gauge set reads adequate pressure, replace pressure switch. Switch can be removed without discharge of refrigeration.
Back switch off in a counter clockwise direction. Re-install in reverse order.
Lubricate o-ring in switch per 21-50-02 page 202. Products, Inc Maintenance Manual 21-50-01 May 15/95 Page 102 7. Check for power at motor. If power is present, proceed to step 8. If power is not present on either pin and load/shed conditions of step 4 are met, check power on the load shed unit at connector Pin 1.
If power is present, system problem exists in load shed system start unit. If power is not present, check 15 amp CB (4) and mode switch (6).
Konica minolta srx 101a. Fault is isolated to compressor/condenser motor. Unit should be replaced.
Select air conditioning OFF, remove electrical power, disconnect service gauge when troubleshooting is complete. Left Evaporator Blower will not operate in high or low speed. Connect ground power to aircraft. Select air conditioning system to ON. Check if power and ground present at fan wire splices and GND terminal strip. If power and ground are present, blower motor (Ref. 21-50-04 IPL Fig.1, item 22) has failed.
Select air conditioning OFF, remove electrical power. Remove blower assy from aircraft. Remove the four screws attaching the motor to the housing.
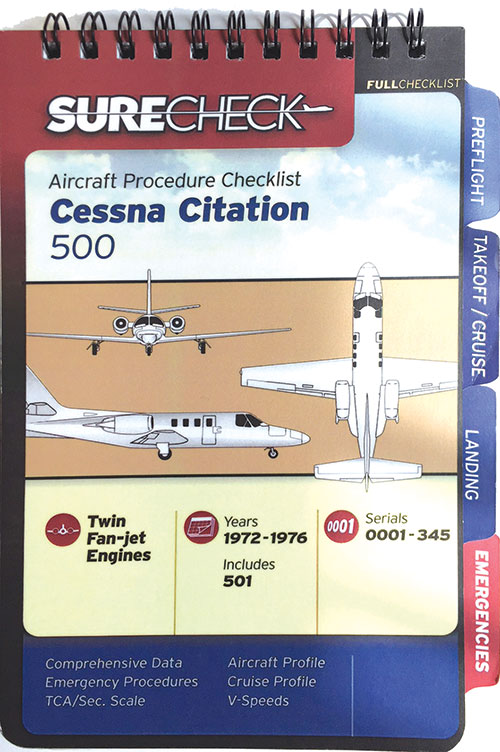
Citation 560xl Flight Manual
Using a 1/8 allen wrench remove blower wheel ( use extreme care not to bend blower wheel). Cut power wires at splice and remove Gnd wire from GND terminal.
Install new motor in reverse order. Left Evaporator Blower will not operate in the low speed setting. Connect ground power to aircraft. Select air conditioning system to ON. Check if power is present at wire EVAP-FL ( at splice). If power is present, the low speed resistor (Ref.
21-50-04 IPL Fig. 1, item 21) has failed. Select air conditioning OFF, remove electrical power. Remove blower assembly and using a #21 drill remove the two rivets securing the resistor. Cut the wires at the splice and remove GND wire from GND terminal. Install new resistor in reverse order.
Right Evaporator Blower will not operate in high or low speed. Connect ground power to aircraft.
Select air conditioning system to ON. Check if power and ground present at fan wire splices and GND terminal strip. If power and ground are present, blower motor (Ref.
21-50-04 IPL Fig.1, item 22) has failed. Select air conditioning OFF, remove electrical power. Products, Inc Maintenance Manual 21-50-01 May 15/95 Page 103 5. Remove blower assy from aircraft. Remove the four screws attaching the motor to the housing. Using a 1/8 allen wrench remove blower wheel ( use extreme care not to bend blower wheel). Cut power wires at splice and remove Gnd wire from GND terminal.
Install new motor in reverse order. Right Evaporator Blower will not operate in the low speed setting. Connect ground power to aircraft. Select air conditioning system to ON. Check if power is present at wire EVAP-AL ( at splice).
Cessna Citation 501 Flight Manuals
If power is present, the low speed resistor (Ref. 21-50-04 IPL Fig. 1, item 21) has failed. Select air conditioning OFF, remove electrical power. Remove blower assembly and using a #21 drill remove the two rivets securing the resistor. Cut the wires at the splice and remove GND wire from GND terminal. Install new resistor in reverse order.
Products, Inc Maintenance Manual 21-50-01 May 15/95 Page 1002 FIG. ITEM PART NUMBER NOMENCLATURE EFFECT UNITS PER ASSY 1 1 2 3 4 5 6 7 8 9 10 11 12 13 14 15 82-75-103 JBS5005-2 MS25361-100 MS3320-15 ES57016-6 ES57016-5 ES57016-3 JBS275-2 JBS13001-1 ES32036-1 JBS11001-1 ES50162-1 MS25036-106 MS25036-156 MS25036-125 Electrical Installation Compressor/Condenser Circuit Breaker Circuit Breaker Switch Switch Switch Blower R/H Blower L/H Grommet Light Indicator Lamp Terminal Terminal Terminal RF 1 ref 1 1 1 1 1 1 ref 1 ref 1 1 1 1 1 1 Air Conditioning System - Electrical System IPL FIGURE 1. Products, Inc Maintenance Manual 21-50-02 May 15/95 Page 1 PLUMBING DESCRIPTION AND OPERATION 1. GENERAL The plumbing system consists of a flexible nylon lined refrigerant hose with permanent swaged on fittings.
All connections are tube O-ring type with sealant on the fitting mating surfaces to ensure leak free operation. Hose, O-ring material, and sealant are specially designed to work with refrigerant R134a and polyol ester oils. Two service valves are located near the compressor/condenser assembly. They are sized differently to avoid incorrect cross-connecting when gaining access to the plumbing for system recharging.
A receiver/drier is installed downstream of the condenser to remove moisture from the liquid refrigerant. A binary pressure switch monitors the refrigerant gas pressure.
This switch will open at a condenser over pressure of 350 psi and under pressured conditions of 30 psi. This will interrupt the power to the compressor control circuit and stop the compressor.
This section of the maintenance manual discusses checks and maintenance practices used for the plumbing portion of the air conditioning system. An Illustrated Parts List is included in Figure 1.